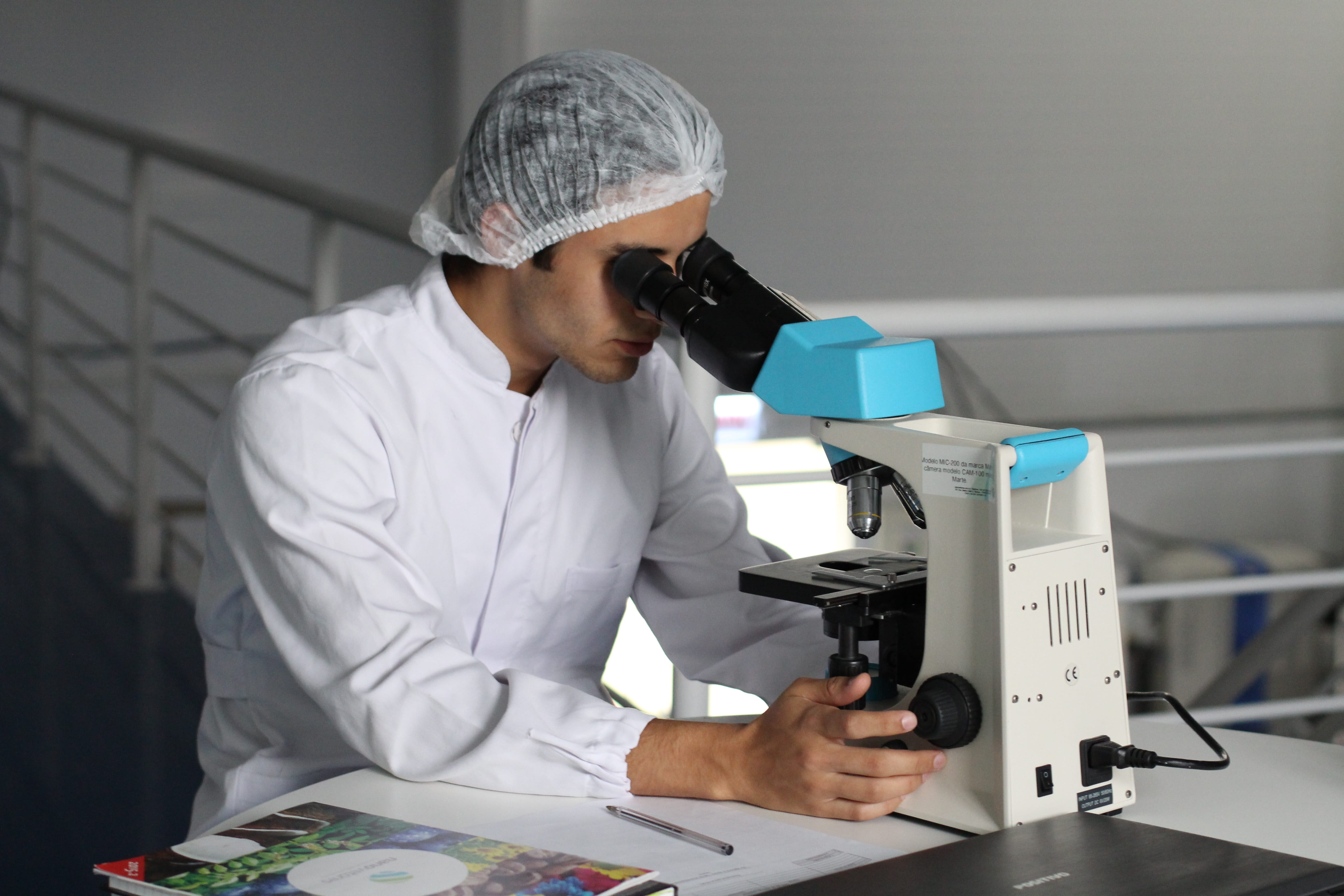
Doing it in stages
Submitted by:
Andrew Warmington
Martin Wuensche and Don Nelson of Albemarle examine the benefits of staging the implementation of a manufacturing intelligence system.
Albemarle is, in many ways, the epitome of a speciality chemicals company, measuring output in both tonnes and grams. Based at Baton Rouge, Louisiana, with 12 manufacturing sites around the world, it produces complex, custom chemicals for pharmaceuticals, agriculture, oil and gas, electronics, metal performance catalysts and more.
Customer expectations are high and Albemarle sets QA standards to exceed them. The company must continually adhere to regulatory requirements and industry standards, including federal, environmental and safety codes, certification protocols and standards, such as those from the American Chemical Council and the European Chemicals Regulation, RC-14001 environmental management systems and ISO standards.
Perhaps the most demanding aspects of speciality chemicals manufacturing, however, lie in the details. Because the chemicals and recipes are unique to each end use, there are numerous specifications and multiple mean parameters that must be monitored throughout the manufacturing process, ranging from complex physical parameters, such as pore size distribution, to trace analysis for chemical impurities.
Continual improvement
Albemarle’s manufacturing processes are finely tuned to small, speciality production; therefore, statistical process control is vital to maintaining quality standards, as well as improving efficiency and consistency. The company practises continual improvement, having adopted a lean manufacturing culture several years ago.
In view of Albemarle’s plans for expansion and acquisition, the Operations Excellence Group (OEG) sought ways to better implement future transition and assimilation, not least because multiple methods of statistical control and production reporting are vital in today’s complex manufacturing environments. The OEG also saw a need in manufacturing to be able to push analysed data from multiple databases in front of production line operators in real time. This would enable operators to access data quickly and easily, monitor process parameters and gain real-time statistical-based insights.
Combining these production needs into one standard for statistical control, monitoring and reporting appeared at first to be a prohibitively complex and expensive proposition. Albemarle was working under a restricted IT budget and limited internal resources. It needed a cost-effective, yet high quality approach that was easy to install and use.
The company has a long relationship with Northwest Analytics (NWA), and so turned to NWA for consultation on manufacturing intelligence software. Together they decided on a pilot programme using NWA Focus EMI. This connects directly to existing data sources, with no data duplication, to deliver real-time process analytics, plus alarm notifications and role-based dashboards.
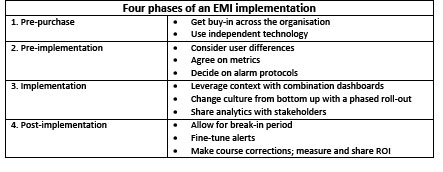
Four phases of implementation
Albemarle takes a pragmatic approach to software deployment, on the basis that it is not desirable to ‘dump it in all at once’ when rolling out software that has potential to change the work culture. The first step, taken prior to the purchase of a software system and perhaps the most difficult, is therefore to get buy-in from across the organisation. Table 1 shows all four stages involved.
To be successful, enterprise manufacturing intelligence (EMI) requires a long-term commitment to collaboration across work sites and job roles. Executives, managers, technical staff, R&D and IT all benefit from the new approach; therefore, the greatest gains are realised when there is support across the company.
However, before going live with EMI, a second step, the pre-implementation phase, is undertaken. Pre-implementation considers roles and responsibilities, and enables a ‘custom fit’ approach to usability. For example, operators make short-term decisions and take quick actions. Directors of operations make long-term decisions and use data to recommend more general course corrections.
As implementation teams consider which metrics are most relevant to processes, they must also consider how the data is used at every level of the organisation and what each user needs in terms of information to do their particular job better. Three types of specialists are needed on an implementation team from the outset: an IT technician who understands hardware issues, someone with broad-based knowledge of general production issues and someone who recognises the power of statistics.
Key performance indicators (KPIs), parameters and responses must also be considered, validated and formalised. It takes a significant amount of work to determine and agree on which metrics are key to monitoring performance from the plant floor to the entire manufacturing enterprise.
This is a challenging process - and one of the most important. It requires representatives from all areas of manufacturing to dive deep into discussions about which measurements matter. And it takes time to consider the data points most important to the process or task, the highly theoretical against practical application, short- and long-term views and acceptable variations in standards (maximum or minimum for required response).
As importantly, a key for success is limiting the number of KPIs being measured and set for alarm. Too many will result in a production team being unable to take action on alarms. This, in turn, can lead a team to become ‘tone deaf’ — ignoring the alarms because they are overwhelmed – and the EMI approach becoming ineffective.
A decision tree (or remediation path) establishes the specific procedures an operator, process engineer and plant manager takes when an alarm presents itself. Developing a decision tree takes users through yes/no questions and the embedded knowledge of the team, which helps balance reaction to alarms. This allows each level of personnel to act and react with the confidence that the action they are taking is the correct one.
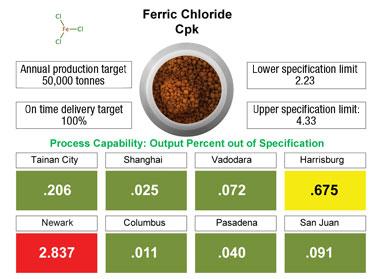
Figure 1: Top level dashboard view across multiple plant locations
For an operator seeing an alarm on a particular process parameter, the action prescribed could be as simple as acknowledging the alarm and notifying the line manager, or it could direct them to acknowledge the alarm and select a course of action from a predetermined pull-down list of options. This speeds the time needed to take action and ultimately enact the correct solution.
Once the difficult but necessary pre-implementation phase is complete, the third step of implementation can commence. Albemarle took a learn-and-adjust approach. Although NWA Focus EMI had been installed at ten manufacturing sites, the company initiated training at a single production plant in Pasadena, Texas. This was done to demonstrate that an EMI approach would be an improvement over current statistical control methods and resolve issues on a small scale before a larger roll-out. It also enabled the company to establish a best practices foundation for replicating and speeding implementation at other sites.
From silos to a single filter
The various manufacturing databases (data silos) were funnelled into NWA Focus EMI’s global analytics layer. Albemarle customised a dashboard (a visual analyser) to work with its Windows-based systems. Into the post-implementation phase, it monitored and resolved issues and made adjustments and corrections as needed.
The initial implementation included training 25 production managers in foundational EMI statistics to bring these first adopters to an expected level of understanding and to identify those who would take ownership over EMI decision-making processes. NWA Focus EMI is now being taken to the operator level, testing the replication of initial implementation and training.
As lessons are learned and applied, each concurrent stage of implementation is that much easier, and makes it more likely that employees will adopt the system quickly. Additionally, demonstrated wins and an ability to provide other plants a roadmap for success not only ensures project buy-in prior to those implementations, but also speeds the adoption of EMI at those plants. This is all part of Albemarle’s self-termed Dynamic Process Control initiative.
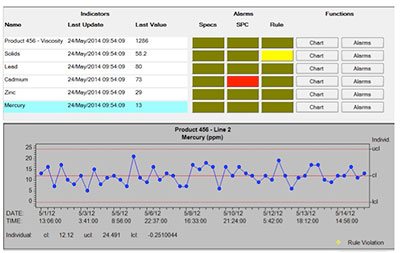
Figure 2: Drilling down from the main dashboard to identify specific issues of concern
Measuring and sharing successes
The main benefits of EMI are the ability to aggregate, analyse and visualise operations-critical information derived from massive amounts of manufacturing data in order to understand issues and take action. Whilst these are the most obvious benefits of EMI, there are many more key indicators of return on investment (ROI), such as the ability to validate the quality of raw materials, supply chain transparency and a reduction in scrap rates.
For Albemarle, a significant ROI came right after initial implementation on a production line. NWA Focus EMI alerted us to a small change in one of several mean parameters that are monitored continually. Unlike some of the others, this one rarely deviates but, when it does, it affects many other production elements. The new system enabled us to determine the root cause of the problem and correct it, much earlier than we would have before.
The benefits of the Dynamic Process Control initiative extend to customers. A technical service failure, such as to oil refining catalysts, can easily be monitored. When a new catalyst is added, the old one is removed and analysed for abnormalities using statistical data rather than observed manually. This allows the technician to fine-tune the catalyst to each customer's requirements and also improve yields.
Measured approach
Albemarle’s initial success with EMI is directly related to its deliberate approach to implementation and its acknowledgement of the collaborative work required prior to system deployment. By following best practices, the company improved its capacity to understand and manage internal processes proactively and its ability to meet the increasing requirements and demands across a dynamic business environment.
With a culture of real-time Dynamic Process Control, Albemarle now has a window into statistical management, a data-driven method for decision-making across production sites. It also sees opportunities to use NWA Focus EMI to address one of its major costs, monitoring energy usage.
Contact:
Peter Guilfoyle,
Vice President, Marketing,
NWA Analytics
Tel: +1 503 224 7727 x113
E-mail: [email protected]
Website: www.nwasoft.com