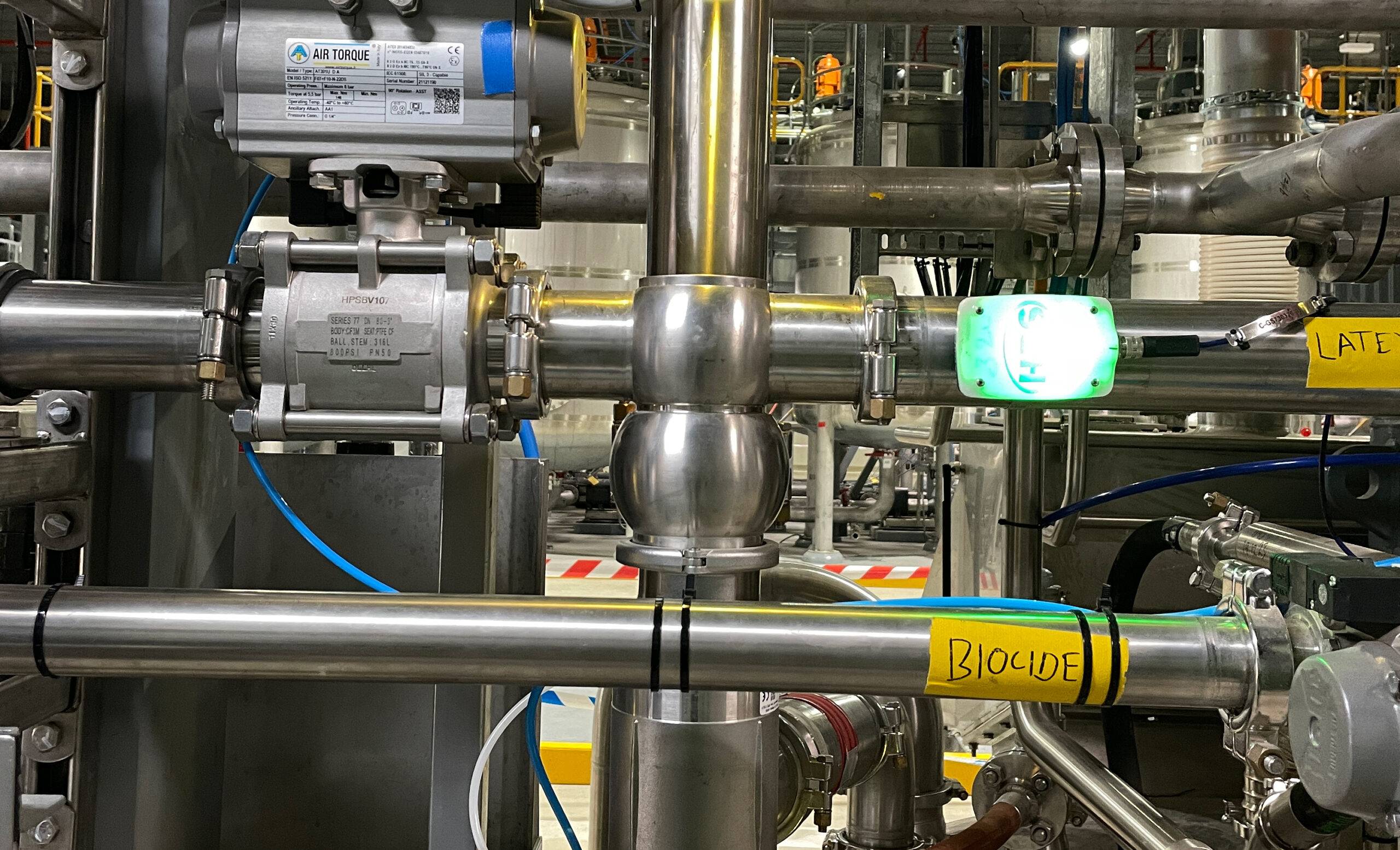
Sponsored content: The hidden cost crisis in chemical manufacturing
Submitted by:
Andrew Warmington
Today’s chemical manufacturers face a multitude of challenges: raw material costs have surged by 18% since 2022; environmental compliance expenses continue climbing (with effluent disposal costs up 22% over five years); and customers increasingly demanding sustainable production practices.
In this high-pressure environment, operational inefficiency isn't just an inconvenience - it's a serious competitive disadvantage. One of the most overlooked sources of these inefficiencies? Pipeline product loss.
Every time product changes occur, traditional cleaning methods like flushing, purging and chemical rinsing leave valuable product behind. This generates excessive waste, increases contamination risks and extends downtime. For speciality chemical producers, these losses can represent significant production volume, directly impacting both profitability and environmental performance.
The solution: HPS pigging technology
Chemical manufacturers across every segment - from commodity chemicals to speciality formulations - are increasingly turning to a proven solution: HPS Advanced Liquid Product Recovery (Pigging) Technology.
This innovative technology uses a specially designed projectile (a ‘pig’) to recover up to 99.5% of residual product from pipelines, transforming what was once inevitable waste into captured value. Implementing this specialist form of technology delivers measurable results across critical performance indicators:
- Yield improvement: Up to 99.5% product recovery from process pipelines
- Waste reduction: 75-90% decrease in cleaning-related effluent volume
- Changeover efficiency: 50-70% faster product transitions
- Water use: Typically 20% reduction in water usage
- Quality assurance: Near-complete separation between product runs
- Payback period: Typically achieved within six to 12 months – then significant year-on-year ROI
What is pigging?
At the core of a pigging system is the pig itself – a projectile made from a flexible, durable and chemically resistant material. Propelled by compressed air, nitrogen or another medium, the pig travels through the pipeline, pushing the product ahead of it to the intended destination.
The pigging process is safe, efficient and completely enclosed, ensuring no exposure to operators or the environment. HPS pigging systems are designed with key features to support demanding chemical applications:
- Compatibility with aggressive chemicals: Pigs and system components are made from materials that can withstand abrasive and corrosive chemicals
- Custom engineering: HPS pigs systems are tailored to fit unique pipeline layouts and process needs
- Safety & compliance: Every system is designed with safety, environmental regulations, and industry standards in mind
Key benefits for chemical manufacturers
HPS pigging systems are specifically designed to address the needs of the chemical processing sector, including the production of paints, solvents resins and speciality chemicals. By recovering up to 99.5% of residual product from pipelines, these systems provide a range of operational, financial and environmental benefits:
- Minimised product loss: Valuable product is recovered rather than flushed to waste, increasing yields and reducing overall losses
- Faster cleaning & changeovers: Although not a replacement for full clean-in-place (CIP) procedures, pigging significantly reduces the time, water, solvent or chemical volumes required for cleaning. This results in faster changeovers and increased production uptime
- Reduced waste & disposal costs: Pigging systems help decrease the volume of flush water, solvents and other waste streams, lowering treatment and disposal requirements
- Lower risk of cross-contamination: A clear physical interface is created between batches, helping to maintain product integrity and avoid contamination
- Improved process efficiency & sustainability: Reduced reliance on water, energy and cleaning chemicals supports both resource efficiency and environmental compliance
- Rapid return on investment: Most chemical manufacturers achieve a return on investment within six to 12 months, driven by higher product recovery, lower cleaning costs and reduced downtime
Key components of a pigging system
A complete pigging system integrates several critical components:
- The pig: A specialist projectile that removes residual liquid from pipelines. Fully detectable, durable and designed for compatibility with chemicals
- Launch, receive & return stations: Also known as pig stations, their main purpose is to introduce the pig safely into the product line, propel the pig to and from source and destination, and store the pig when it’s not in use.
- Pig housing: When the pig is not in use, it resides in a special housing called the pig housing, which is slightly larger than the pig to enable CIP.
- Pig detectors: Track the pig’s location in real time for accurate, controlled operation and process safety.
- Control system: Manages the pigging sequence through PLCs or integrated automation, reducing manual intervention and improving efficiency.
- Valves & actuators: Direct product, propellant and pig flow, configured for your process layout and materials.
Proven success across chemical sectors
Case study 1: European silicone gel manufacturer
This company encountered significant product loss and cross-contamination during manual pipeline flushing. Residual gel mixed with subsequent products, leading to costly disposal and quality concerns.
The HPS solution was two fully automated pigging systems, enabling near-complete product recovery and reducing contamination risk to nearly zero. The result: lower disposal costs, improved yield and increased overall productivity.
Case study 2: US chemical producer
The large-scale facility experienced considerable waste—approximately 60 gallons (273 L) of product lost per changeover, totalling $5 million/year. Prolonged cleaning cycles also limited production capacity.
HPS pigging recovered most of the residual product, reduced downtime, and significantly lowered cleaning and disposal costs. The system paid for itself within weeks of implementation.
Case study 3: Speciality chemical manufacturer
A major chemical production facility in Louisville, Kentucky, faced challenges with product losses during batch changeovers—approximately 19 gallons (86 L) of product were being wasted per batch. This amounted to an estimated $48,000/year in product loss alone.
HPS provided a 3-inch (7.6 cm) Schedule 10 Pigging System to recover residual product, cut waste and speed up changeovers. Additional savings are expected from reduced water and disposal costs, delivering a fast payback and high ROI.
Case study 4: Sustainability in paint manufacturing
An independent report analysing water- and solvent-based paint production found that pigging reduced carbon emissions by 2.6 tonnes CO2 eq./ changeover. For sustainability-focused companies, pigging delivers both financial and environmental value.
A future-proof solution
As the industry faces ongoing challenges from shifting regulations, tariffs and economic uncertainties, the need for adaptable, future-proof production systems has never been greater.
Pigging technology is much more than a short-term fix; it’s a long-term investment that provides consistent savings and improved efficiency over time. With the ability to scale and adapt to changes in production needs, pigging systems help manufacturers stay competitive in a rapidly changing market.
Beyond pigging: Comprehensive liquid transfer optimisation
For manufacturers seeking to maximise efficiency across their liquid processing operations, HPS offers complementary technologies that enhance the value of pigging systems.
Liquid routing manifolds: Precision control for complex processes
Chemical facilities dealing with multiple product formulations benefit from integrated routing solutions that eliminate transfer errors while maintaining product integrity. HPS liquid routing manifolds deliver:
- Better control: Ensure precise routing and reduce the risk of costly errors or misdirected transfers.
- Optimised space: Eliminate the need for multiple dedicated lines or cluttered hose arrangements
- Seamless changeovers: Easily switch between products or lines while minimising cross-contamination.
- Increased efficiency: Maintain continuous production with fast routing and fewer delays
Automatrix: Fully automated valve manifold
The HPS Automatrix is an advanced, fully automated valve manifold that is ideal for hygienic and industrial chemical processes. It enables fully automated selection of sources and destinations, providing a fast, safe and reliable way to route liquids with minimal operator input.
With an exceptionally flexible design, the Automatrix is available in horizontal or vertical formats and is easily expandable as processing needs evolve. It’s especially well suited to facilities seeking to eliminate manual routing, reduce human error and increase throughput, while maintaining rigorous hygiene standards.
When integrated with HPS pigging technology, the Automatrix maximises product recovery with minimal product loss throughout the transfer process
Rotomatrix: Manual piggable manifold
For a more cost-effective yet highly efficient solution, the HPS Rotomatrix offers a manually operated routing system with full piggability. Its compact, rotating arm design enables quick and reliable source-to-destination connections, with interlocks for safety and process control.
Ideal for facilities making products such as paint, coatings, chemicals and more, the Rotomatrix enables full product recovery while minimising downtime and misrouting risks. It’s available in a range of sizes and configurations to suit unique process requirements.
Expert Implementation: The HPS difference
With over three decades of specialised expertise and more than 2,000 successful system installations globally, HPS product recovery solutions offers extensive experience in chemical manufacturing applications. The company’s approach combines engineering precision with practical implementation knowledge, delivering end-to-end solutions that perform reliably and efficiently:
- Comprehensive process assessment: In-depth analysis of existing operations, challenges and areas for improvement
- Custom system design: Bespoke engineering solutions including single, double, dual-pig configurations tailored to product characteristics, process demands, and facility layouts
- Seamless implementation: Proven installation methodologies that minimise disruption to ongoing production
- Commissioning & training: Full system commissioning, testing and operator training to ensure safety, reliability and performance from Day One
- Ongoing support: Dedicated technical support and optimisation services across the system lifecycle
Pigging technology continues to represent a proven, low-risk investment for chemical manufacturers aiming to enhance product recovery, reduce waste, maintain product quality and improve operational capacity. By integrating HPS advanced pigging technology into liquid transfer processes, chemical facilities can realise measurable gains in efficiency, sustainability and cost-effectiveness.
Process Pigging Technology Experts
HPS Product Recovery Solutions